LadyHawkeAvry
Songster
I have built several coolerbators, and despite the family buying me a Brinsea, I still have my active coolerbator in constant use. I had grown out of just two incubators, lhowever, and needed to build a third. I decided "Go big or go home", and set my sights on a cabinet. I searched Craigslist for building materials, and was less than thrilled with the results. I had found several non working beverage coolers, all obscenely overpriced, and most wine coolers were too small. After a few months, I finally found a 3.5 cu. ft. Haier wine chiller, which became the base for the build.
Parts:
Wine chiller
Electrical wire
Extension cord or replacement lamp cord with plug
Small transformer plug
Wire conduit
Ceramic light fixtures
60 watt light bulbs
120 mm computer fans
High temperature sealant
2 x 4 x 6
1" wide wood strips (or smaller)
STC-1000 temperature controller
Caulk
assorted screws
Duct tape
clear aquarium tubing
hardware cloth
insulation board
silver solder
wire nuts
shelving or similar material
Rubber gaskets or bushings (small)
Tools:
Dremel with cutoff wheel
drill
circular saw
soldering iron
assorted drill bits
small screwdrivers (both phillips and flat head)
large screwdrivers (both phillips and flat head)
wrenches
vise grips
pipe cutter
drum sander for Dremel
hole saw
Day 1:
The compressor and original thermostat were removed from the cooler. This is best done outside or in a garage with ventilation, as the coolant gas inside the system is toxic and will escape as the lines are cut.
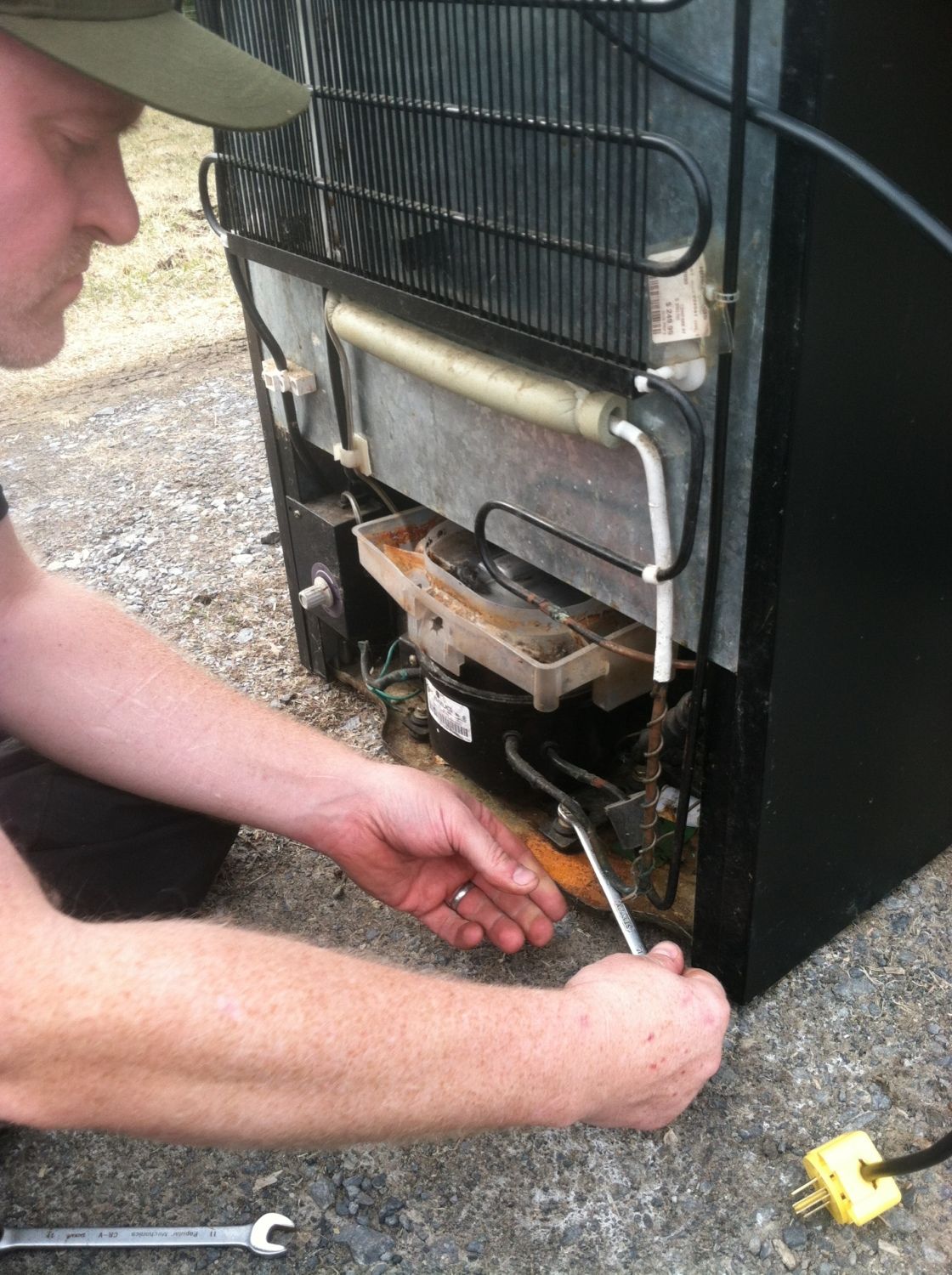
removing the bolts from the compressor

Unhooking the electronics

Removing the thermostat and temperature control unit

With the thermostat and electronics removed, the rear bolts can be accessed
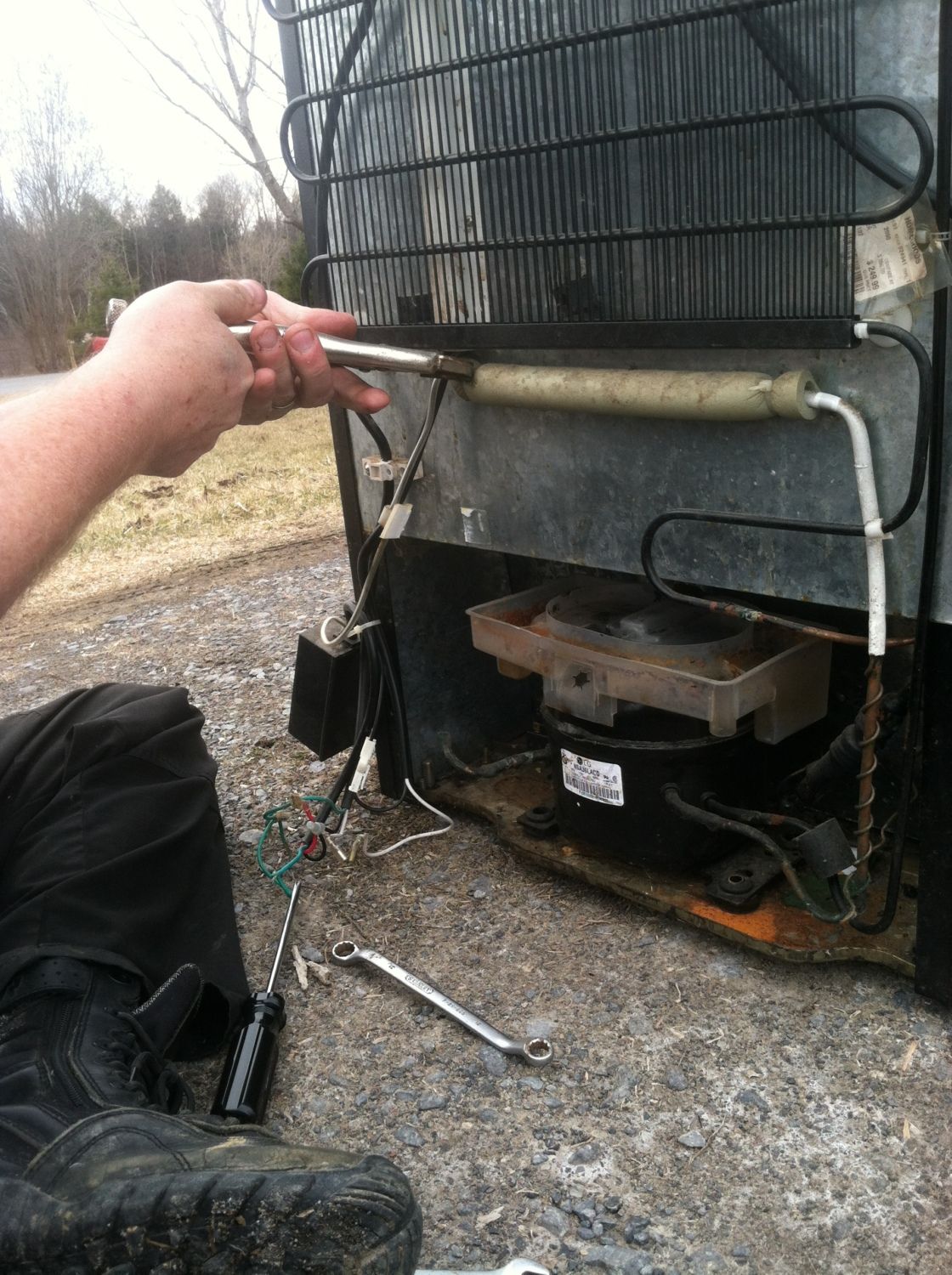
Removing the hoses and insulation

Cutting through the aluminum hoses with a pipe cutter allows for removal of the cooling grille. Freon gas will escape when this line is cut, and breathing it should be avoided.

Once the grille is removed, the remaining lines can be cut and the compressor removed

The remaining hoses and wires can now be removed from the back before starting on the inside

The refrigerator plate from the inside is then removed, and the unit is ready for cleaning.

Once scrubbed and bleached, the cooler was ready to head inside for assembly into an incubator.
Parts:
Wine chiller
Electrical wire
Extension cord or replacement lamp cord with plug
Small transformer plug
Wire conduit
Ceramic light fixtures
60 watt light bulbs
120 mm computer fans
High temperature sealant
2 x 4 x 6
1" wide wood strips (or smaller)
STC-1000 temperature controller
Caulk
assorted screws
Duct tape
clear aquarium tubing
hardware cloth
insulation board
silver solder
wire nuts
shelving or similar material
Rubber gaskets or bushings (small)
Tools:
Dremel with cutoff wheel
drill
circular saw
soldering iron
assorted drill bits
small screwdrivers (both phillips and flat head)
large screwdrivers (both phillips and flat head)
wrenches
vise grips
pipe cutter
drum sander for Dremel
hole saw
Day 1:
The compressor and original thermostat were removed from the cooler. This is best done outside or in a garage with ventilation, as the coolant gas inside the system is toxic and will escape as the lines are cut.
removing the bolts from the compressor
Unhooking the electronics
Removing the thermostat and temperature control unit
With the thermostat and electronics removed, the rear bolts can be accessed
Removing the hoses and insulation
Cutting through the aluminum hoses with a pipe cutter allows for removal of the cooling grille. Freon gas will escape when this line is cut, and breathing it should be avoided.
Once the grille is removed, the remaining lines can be cut and the compressor removed
The remaining hoses and wires can now be removed from the back before starting on the inside
The refrigerator plate from the inside is then removed, and the unit is ready for cleaning.
Once scrubbed and bleached, the cooler was ready to head inside for assembly into an incubator.
Last edited: